Optimizing recipes using data
The Smart Maintenance Techport fieldlab focuses on applying different types of measurements with sensors to determine the condition of an installation. How this works in practice is now being experienced at Beitsbaan 22 of asset-owner Tata Steel IJmuiden. IJssel and Semiotic Labs have installed their sensors and the first data are being collected. During the next scheduled maintenance, SKF's sensors will be added.
Hans Sintemaartensdijk: "My dream is a dashboard that shows at a glance whether the machine is happy or not, no matter what product is being run."
Visualizing variables
Within the field lab, a project on the Pickling Line 22 was chosen because it has many variables and there is not yet enough insight into how the different bridles function separately from each other and in conjunction under different conditions. The sensors of Semiotic Labs measure electrical signals from the switch box, the sensors of IJssel and SKF measure the vibrations of the track itself. The varying load on the bridles from the different steels makes it interesting to see how the sensors return the interplay between the bridles. Derek Benner of Semiotic Labs: "We know, for example, that at certain times the steel drives the motors instead of the other way around. With the data from the sensors, we are now able to map how and when this happens and what the effect is."
Derek Benner: "Combining different measurement techniques gives a broader picture of failure mechanisms and what their effects are. The techniques reinforce each other and that becomes visible."
Broad involvement
The sensors from IJssel and Semiotic Labs were installed in close cooperation with the company chief, maintenance manager and engineers. Hans Sintemaartensdijk: "The enthusiasm within the project is great, few words are needed to get a lot done. We decide together what we want to investigate, and the research question keeps forming as we go along." David Andreas van IJssel adds, "A lot comes together in the project. The employees are interested in what we are doing and in the potential. Many operators have a feeling for what is going on on the job and want to know what they will soon see reflected in the dashboard." Derek concurs: "Partners work well together, we get together a lot so you get to know each other, each other's product and also your own product better. What we're doing at 22 Pickling Lane is really new."
David Andreas: "We are exploring new territory together and learning by doing. This collaboration goes beyond our own system."
Combining data
Through wireless 4G connection, the sensors are connected to the cloud and the data becomes visible in now different dashboards. Derek on this approach: "Within the field lab, we share the data from the sensors with each other and we can compare and optimize different techniques. And it's an interplay with the process operators. The combination of their process knowledge and our knowledge of condition monitoring puts us in a good position to map failure mechanisms." The next step is to combine the data from the various sensors into a dashboard to see at a glance how the whole thing is performing. Hans describes it as optimizing the recipe. "If you know what is running smoothly and what is not, you can respond to this with specific actions. The first results are already visible. A phenomenon became visible from the graphs that we can now look at further in a focused way." David: "We all see part of the spectrum and the question is, are we seeing the same thing from the different signals. A lot is still needed for this, think for example of synchronization, but that is the phase we are entering now."
The dashboard is being developed in close cooperation the Amsterdam Center for Business Analytics (ACBA), part of the VU, which is also a partner of the field lab. Could Hans Sintemaartensdijk's dream become reality? We will keep you posted.
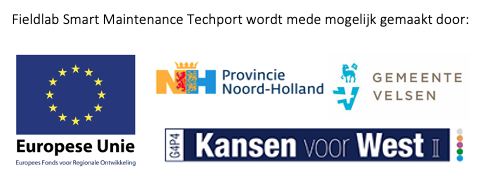